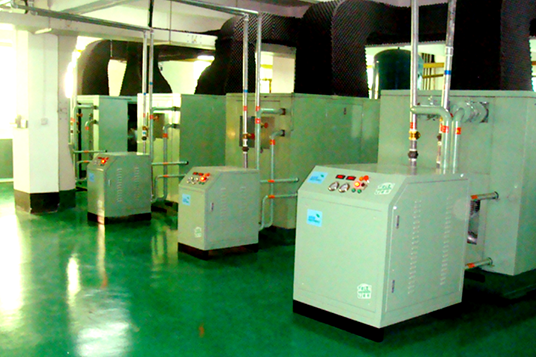
1、 Application scenario analysis
The food and beverage industry has extremely strict hygiene and safety requirements for compressed air, ensuring that it is oil-free, sterile, and odorless to prevent contamination of food and beverage products. In addition, the gas demand during the production process is relatively stable, but there are high requirements for the stability and continuity of the gas supply pressure. Traditional air compressor systems often face issues such as high energy consumption, complex maintenance, and difficulty in ensuring gas supply quality when meeting these special requirements.
2、 Energy saving engineering solutions
Selection and installation of food grade air compressors
Select screw air compressors or piston air compressors that meet the hygiene standards of the food industry. These air compressors use food grade lubricants or oil-free lubrication technology to ensure that compressed air does not contaminate food and beverage products. At the same time, the air inlet of the air compressor is equipped with an efficient air filter, which can effectively filter impurities, microorganisms, and odors in the air, ensuring the quality of the air entering the air compressor.
Reasonably allocate the number and capacity of air compressors based on the production scale and gas demand of food and beverage factories. Adopting a one for one backup or multiple parallel operation mode to ensure stable gas supply in any situation. Moreover, when selecting the installation location of the air compressor, consideration should be given to a well ventilated, dry, and clean environment, which facilitates the heat dissipation and maintenance of the air compressor.
Compressed air purification and disinfection treatment
Build a comprehensive compressed air purification system, including precision filters, activated carbon filters, sterilization filters, and other equipment. Precision filters can remove small particles and oil mist from compressed air, activated carbon filters can adsorb odors and organic impurities, and sterilization filters use efficient sterilization technology to ensure that the microbial content in compressed air meets food industry standards.
In order to further ensure the hygiene and safety of compressed air, ultraviolet disinfection or ozone disinfection technology is used to regularly disinfect the compressed air. Disinfection equipment is installed at appropriate positions in the compressed air pipeline system, with disinfection time and frequency set according to production process requirements and hygiene standards, effectively killing bacteria, viruses, and other microorganisms in the compressed air.
Energy saving operation and monitoring management
Install an energy-saving controller for the air compressor to achieve intelligent operation control of the air compressor. The energy-saving controller automatically adjusts the load rate and start stop status of the air compressor based on changes in gas pressure and flow rate on the production line, avoiding prolonged operation of the air compressor under no-load or low load conditions and improving energy utilization efficiency. For example, during production intervals or when gas demand is low, the speed of the air compressor is automatically reduced or some air compressors are stopped. When gas demand increases, normal operation is quickly restored and load distribution is adjusted.
Establish a monitoring and management platform for compressed air systems to monitor in real-time the operating parameters of air compressors, the working status of purification equipment, and the quality indicators of compressed air. Through the monitoring platform, management personnel can promptly detect equipment failures, abnormal gas supply, and other issues, and take corresponding measures to deal with them. At the same time, the monitoring platform also has data analysis functions, which can statistically analyze the operating data of the air compressor system, providing a basis for optimizing equipment operation and energy-saving management.
3、 Energy saving effect estimation
After implementing this energy-saving engineering solution, the energy consumption of air compressor systems in the food and beverage industry can be reduced by 15% -25%. Stable gas supply quality will ensure the hygiene and safety of food and beverage products, reduce product quality problems caused by compressed air pollution, and increase product qualification rate by about 3% -5%. In addition, through the implementation of energy-saving operation control and monitoring management measures, the energy management level of enterprises will be significantly improved, which will help reduce operating costs and improve production efficiency.