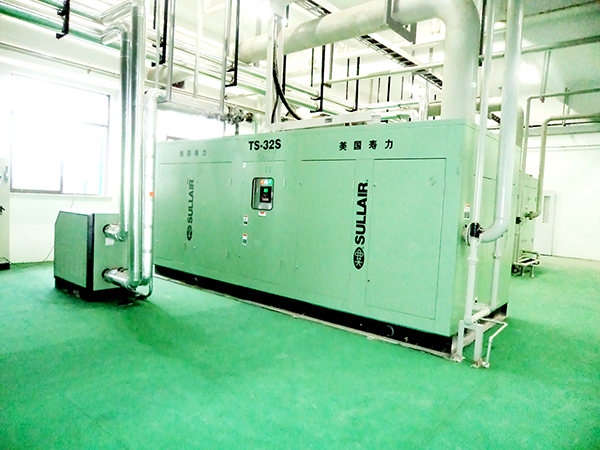
1、 Application scenario analysis
Electronic and electrical factories have extremely high quality requirements for compressed air, requiring pure compressed air free of oil, water, and dust to ensure the production quality of electronic products. At the same time, there are numerous and precise gas equipment on the production line, which require strict stability of gas supply pressure and flow rate. Traditional air compressor systems often suffer from serious energy waste, high equipment maintenance costs, and unstable gas supply quality when meeting these requirements.
2、 Energy saving engineering solutions
Selection and configuration of oil-free air compressor
Choose oil-free screw air compressors or centrifugal air compressors to ensure that the quality of compressed air meets the high standards required for electronic and electrical production. These oil-free air compressors use special sealing and lubrication technologies to avoid contamination of compressed air by lubricating oil, reduce the burden on subsequent purification equipment, and improve overall energy utilization efficiency.
According to the gas consumption scale and characteristics of the factory, multiple low-power oil-free air compressors are operated in parallel. This can achieve more precise air volume regulation by turning off some air compressors under partial load conditions, avoiding the high energy consumption problem of a single high-power air compressor at low loads. At the same time, the parallel operation of the air compressor system has higher reliability. When one of the air compressors fails, the other air compressors can still maintain normal gas supply, ensuring production continuity.
Compressed air precision purification system
Build a comprehensive compressed air precision purification system, including multi-stage filters, refrigerated dryers, adsorption dryers, and other equipment. The filter adopts efficient filter material, which can effectively remove small particles, oil mist and moisture in compressed air, ensuring that the cleanliness of compressed air reaches below 0.01 μ m, the oil content is below 0.01ppm, and the dew point temperature is below -40 ℃. The refrigerated dryer and adsorption dryer work together to automatically switch working modes according to different working conditions and gas requirements, achieving efficient dehumidification and drying functions while avoiding energy waste.
Install compressed air quality online monitoring device to monitor various quality indicators of compressed air in real time. Once the quality of compressed air is found to have decreased, the system immediately starts the corresponding purification equipment for processing, ensuring that the gas equipment on the production line always receives high-quality compressed air supply.
Intelligent energy-saving control system
Introduce advanced intelligent energy-saving control systems to unify the management and monitoring of air compressors and purification equipment. The system collects real-time operating parameters such as pressure, flow rate, and temperature of the air compressor and the working status information of the purification equipment through sensors, and uses intelligent algorithms for data analysis and processing to achieve optimized operation control of the air compressor. For example, according to the changes in gas consumption on the production line, the load rate and number of operating air compressors are automatically adjusted to ensure that the air compressors always operate in an efficient and energy-saving state. At the same time, the intelligent control system also has remote monitoring function, which facilitates factory management personnel to grasp the operation status of the air compressor system anytime and anywhere, and timely issue fault warnings and handle them.
Adopting energy recovery technology to recycle and utilize the heat generated during the operation of the air compressor. The recovered heat can be used for the factory's air conditioning system or process heating process, improving the comprehensive utilization efficiency of energy and further reducing the factory's energy consumption.
3、 Energy saving effect estimation
By implementing the above-mentioned energy-saving engineering solutions, the energy consumption of the air compressor system in electronic and electrical factories is expected to be reduced by 20% to 30%. Stable gas supply quality will effectively improve the yield rate of electronic products and reduce the scrap rate by about 2-3%. Meanwhile, due to the adoption of intelligent energy-saving control systems and energy recovery technologies, the energy costs of enterprises can be further reduced by about 5% -10%, providing stronger cost advantages and quality assurance for enterprises in fierce market competition.